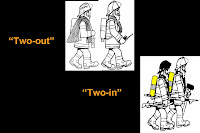
If you do not have two firefighters for entry, and two for a safety line, you do not enter an aircraft (or structure). I work at a Index A airport, working under Part 139 rules and regulations. Staffing is not mentioned in the 139, only extinguishing agent requirements. After normal working hours and weekends, we may have three ARFF responders, in the evening two, and overnight one. With this being said our operation can run into some hard decisions. Your own safety comes first, but your intuition as a firefighter is to help those in need.
You and your partner respond to a aircraft accident, people are in the aircraft that can't get themselves out. Mutual Aids are five minutes or more away, what do you do? Risk over Benefit...
Are you putting yourself in danger? Are you following policies and procedures? Are you going to be disciplined?
Are you going to sit there and watch people in need, while you wait for two or three other responders to arrive? Is putting the "wet stuff on the hot stuff"(water on fire) going to be sufficient. Is putting the "White stuff on the red stuff" (foam on fire) going to be enough for you to feel like to gave it your all.
I don't claim to have the answers to all these questions. As Firefighters you are up against a hard task. Aircraft burn very fast, within 90 seconds it could burn to ashes. Aviation fuels are very dangerous to handle. As the people are running away, we are running in.
As you make decisions based on this topic, think them through. Start today, when an aircraft emergency may arise it should not be the first time this topic was discussed.
We all have families that want us to come home the way we left. Review your Operating Guidelines, talk with the people on your shift, have a plan in place for when it happens.
You and your partner respond to a aircraft accident, people are in the aircraft that can't get themselves out. Mutual Aids are five minutes or more away, what do you do? Risk over Benefit...
Are you putting yourself in danger? Are you following policies and procedures? Are you going to be disciplined?
Are you going to sit there and watch people in need, while you wait for two or three other responders to arrive? Is putting the "wet stuff on the hot stuff"(water on fire) going to be sufficient. Is putting the "White stuff on the red stuff" (foam on fire) going to be enough for you to feel like to gave it your all.
I don't claim to have the answers to all these questions. As Firefighters you are up against a hard task. Aircraft burn very fast, within 90 seconds it could burn to ashes. Aviation fuels are very dangerous to handle. As the people are running away, we are running in.
As you make decisions based on this topic, think them through. Start today, when an aircraft emergency may arise it should not be the first time this topic was discussed.
We all have families that want us to come home the way we left. Review your Operating Guidelines, talk with the people on your shift, have a plan in place for when it happens.
Not If It Happens, When It Happens!!!